Cleaning and lubricating the sewing machine parts extends the life of the entire device. And although it is impossible to completely get rid of the natural wear of the mechanisms, it is possible to increase the machine's service life by an order of magnitude. Along with the service life, less noise, smoother running, even seams and a clear choice of operating mode become satisfactory.
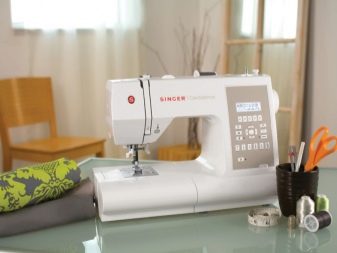
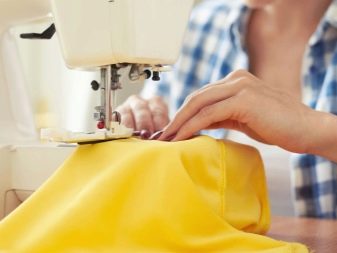
Why and how often should I lubricate?
A sewing machine, unlike a stapler stapler, needs periodic cleaning and lubrication. The friction force of the parts contributes to their wear. If you forget to grease the machine and continue to work on it, soon they will completely wear out and fail, first of all, those parts that are under the greatest load. The friction force - and with it the abrasion of parts - can be reduced several times if you use grease.
When the machine operates in heavy duty (constant load) every day, monthly cleaning and lubrication of all mechanisms involved in the work is necessary. With rare work (for example, once a week for half an hour or an hour), parts are cleaned and lubricated at least once a quarter.
The dependence of the lubrication frequency of the parts on the total output (how many hours the mechanisms worked) is non-linear - this is due to the accumulation of dust on the parts, which settles on the mechanisms, is attracted to the parts.
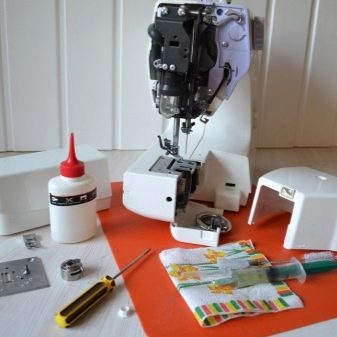
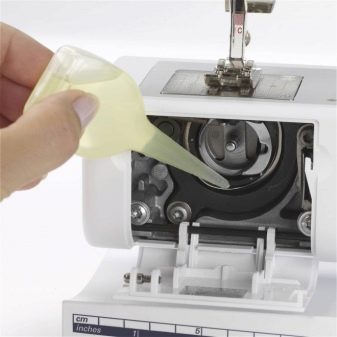
What can be used for lubrication?
Oil suitable for lubricating sewing mechanisms, door locks and similar mechanics is industrial only. It has a special composition that is light and fluid enough that dust and metal particles (scraping from parts during operation) do not create a sticky and viscous substance with it.That, in turn, significantly slows down the rotation and the reciprocating movement of the moving elements.
The use of other oils is unacceptable.
- Vegetable oil evaporates quickly when parts become warm from abrasion during long work. It is easily oxidized and decomposed in the open air and at a slightly higher temperature than room temperature.
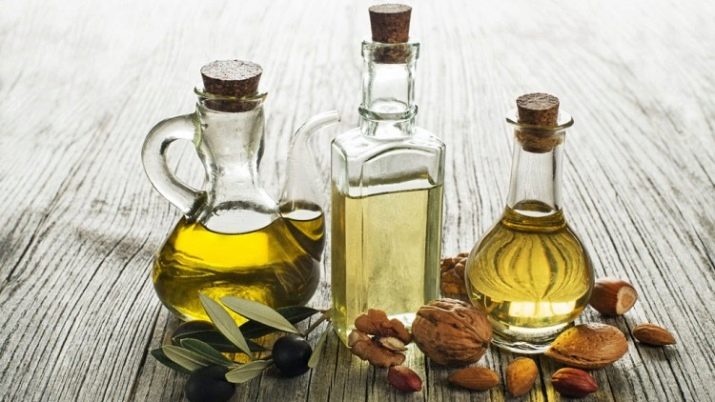
- Animal fats - butter, butter, and similar products are also subject to accelerated evaporation. The more refractory fat is used, the faster the oil-sticky coating forms, half of which is formed by solid particles. And the fat itself, hardening, will add to the typewriter of "low-speed".
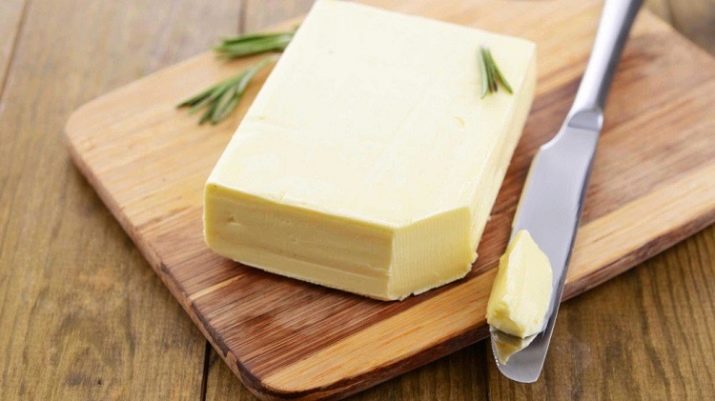
- Motor oil. If your choice still fell on engine oil, choose a composition with a lower viscosity for summer driving. The fact is that the sewing machine is likely to be used at home and warm even in winter, and not in the cold in the gazebo, so it makes no sense to use “winter” and excessively viscous oils. But this is an extreme option. It will come in handy when there is no way to go urgently for a bottle of “door” oil, but the work is worth it and it is urgent to continue it.
Lithol and solid oil are also not recommended for use (nylon gears are the exception), but graphite-containing lubricant is partially suitable.
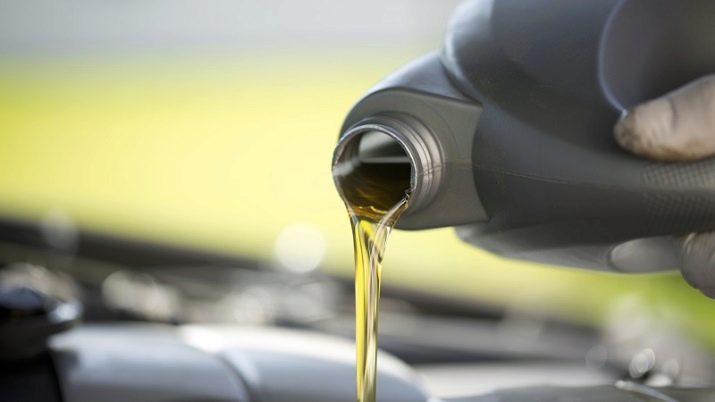
- Oil processing. Its structure is broken. Fatty hydrocarbons used as lubricating oils lose their properties, including water-repellent ones. They evaporate many times faster than fresh engine oil.
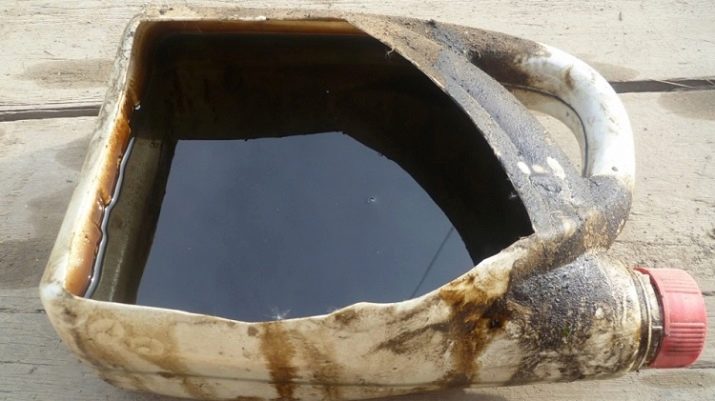
To check how a “third-party” lubricant behaves, lubricate the bike chain and try to drive a hundred kilometers on such a bicycle. After a few tens of kilometers, oily sticky dirt formed by dust with such a lubricant will become viscous like tar. As a result, the pedals will turn with a noticeably greater effort than with chains and sprockets lubricated with industrial oil, as if you were going uphill. The machine will behave in the same way - the sewing speed may decrease by two or more times.
In principle, the purpose of the oil is to prevent wear and rust of parts. Any oil does not allow water (steam, spray) to the parts. While the machine works easily, any composition is acceptable.

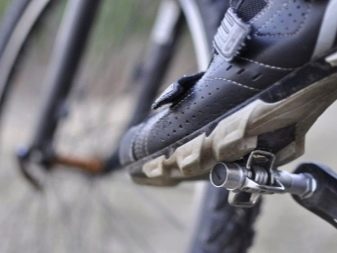
But as soon as you notice that the speed of the machine began to fall (for example, by the frequency of the tap of the needle bar mechanism and the clicks of the shuttle, the “howling” of the engine) - wait a bit with the work:
- disassemble the machine;
- clean and lubricate its mechanisms;
- then reassemble it.
And yet, so as not to waste time unnecessarily disassembling and lubricating parts, use special oil for cars and locks.
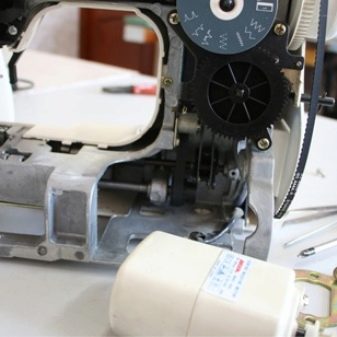
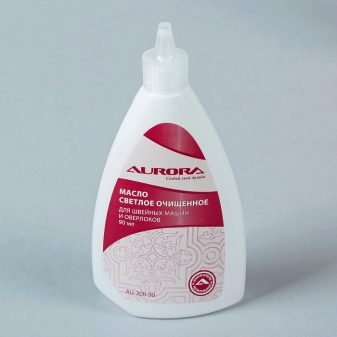
Description of procedure
The whole procedure for bringing the sewing mechanisms in a sanitary state is divided into several stages.
- Scroll drive shaft to the topmost needle bar position and unplug the machine.
- Remove the upper and lower threads from the machine (all, no matter how many there were at the time of interruption) and free the stapler from the stitched fabric.
- Remove the case, guided by the maintenance instruction (is included in the package).
- Clean moving parts of plaque formed by moving threads and dust. The needle plate, the fabric guide teeth, the needle bar mechanism with the foot and the shuttle assembly are checked (and cleaned if necessary). It is also necessary to check the condition of the gears. If you suspect a "tight" motor operation, the engine itself is disassembled. Its bearings are cleaned, lubricated and re-set according to the level of the shaft. An old machine that does not have an electric motor and is driven by a hand or foot rotator is disassembled, cleaned and lubricated in the same way.
- Lubricate all rubbing surfaces. In this case, it is advisable to rotate the drive shaft - this will make sure that the mechanism is fully lubricated. So, the shuttle requires only a few drops of oil.The gears and motor oil can take a little more - make sure that all friction surfaces are evenly covered with a thin layer of engine oil. For a point dosage, a syringe with a needle will do.
- Reassemble the machine and drive it idle.
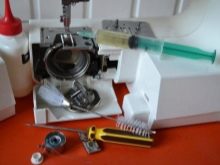
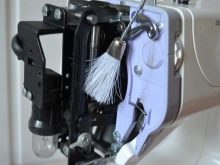
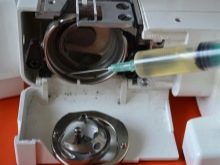
It does not matter the type of product - manual (or foot) or electric drive, The approximate step-by-step instruction is correct and uniform. But in some models the case is tight enough - the moving parts are protected by gaskets and anthers, and in its right places there are technological openings closed with plugs.
After lubrication and assembly, you can refill the threads again (in accordance with the instructions for the product), set the desired tensioner settings, insert layers of fabric under the presser foot and continue previously broken seams.
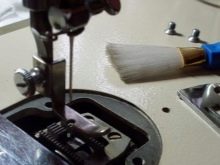
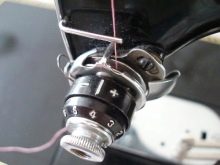
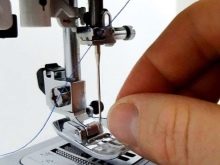
General care recommendations
Cleaning and lubricating the machine is an effective measure that protects it from damage, but it is still half the battle. So that the cleaning does not become unscheduled or does not turn into what you “overlooked”, which you did not pay attention to in time, the machine itself must be kept clean. In addition to external cleaning of the housing and outward-facing mechanics, a number of other recommendations should be followed.
- Use fabrics and threads without excessive "hairiness".
- Threads should be stretchable enough - this will prevent them from breaking apart during sewing.
- Measure the size of the needles and the thickness of the thread with the stiffness and thickness of the stitched layers of matter.
- Provide the necessary for specific threads and fabrics tightening the tensioner of the upper and "bobbin" threads. Check this parameter when changing the thread, needle and fabric - a mismatch will lead to pulling, pulling the matter into the hole of the needle plate or to fragility, skew, “sagging” stitches.
- Do not break the order of transmission of threads, described in the user manual of this device.
- Parts and mechanisms can be cleaned with a soft, flap-free cloth. In the absence of such rags, spent cotton wool, a bandage or other material will do. But the remaining villi need to be removed anyway, in which tweezers can help you.
- When cleaning, it is permissible to use alcohol, gasoline, kerosene or diesel fuel. However, the lubricating oil should be applied immediately - without lubrication, the just cleaned parts will quickly dry and work “dry”, which will lead to their complete wear in just an hour or three intensive work.
- If any of the parts is still worn out, then Do not work with a defective mechanism. Not every owner understands in detail the maintenance and repair of the sewing machine (and other similar devices). Ignoring the replacement of a failed component, it is easy to provoke a failure and several others that interact with it directly (or not). The best way out is to contact the service center for the repair of sewing, knitting and embroidery equipment.
Observing all the above recommendations, you can always maintain the machine in a fully operational and efficient condition.
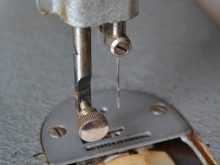
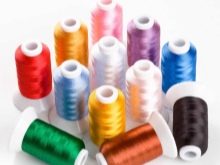
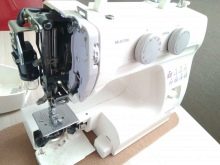
See how to lubricate a horizontal shuttle sewing machine in the next video.