Nowadays, the work of a locksmith has become one of the most common manufacturing specialties in our country. This is due to the great demand and the existence of many narrower specializations in this direction. One example of this was the position of a toolmaker. In our article we will dwell in detail on the features of this profession, labor duties, as well as the competencies and skills that this employee should possess.
Features
High quality production of all kinds of tools, dies and instruments is one of the necessary conditions for efficient production at each engineering enterprise. Without the correct technological equipment, it is not possible to produce machines, machines and other equipment, as well as it is unrealistic to achieve high indicators of labor productivity and product quality.
The instrumental units are not related to the main workshops, but rather to the auxiliary ones. In practice, this workshop takes only an indirect part in the overall technological cycle of the plant.
His tasks include not directly production, but the creation of the conditions necessary for him. However, this fact does not detract from the importance of tool makers in the overall production process of the company.
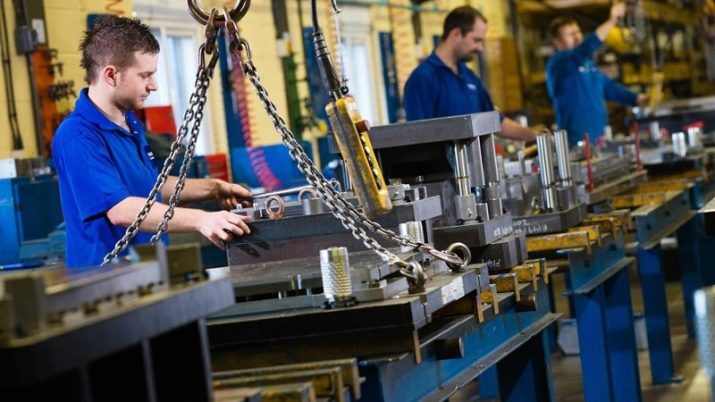
The instrumental business of any enterprise is much more complicated and more accurate than the basic one, which is why specialists in this field belong to the most qualified part of working specialties. At the same time, the toolmaker is much more laborious and diverse of all instrumental professions - this person carries out work that cannot be performed on the most accurate and technologically advanced equipment. This worker is responsible for assembling cutting and measuring tools, as well as apparatuses, dies and instruments, performs their metalwork and finishes the cleanest and finest surfaces. As a rule, the number of locksmiths is about 35% of all workers in the tool division.
The undoubted advantages of this specialty include:
- widespread demand for workers;
- employment in a wide variety of manufacturing sectors;
- good prospects for professional growth and career building;
- the possibility of mastering the specialty directly in production;
- high level of remuneration.
However, it was not without minuses. Among them are:
- increased physical activity;
- hard working conditions.
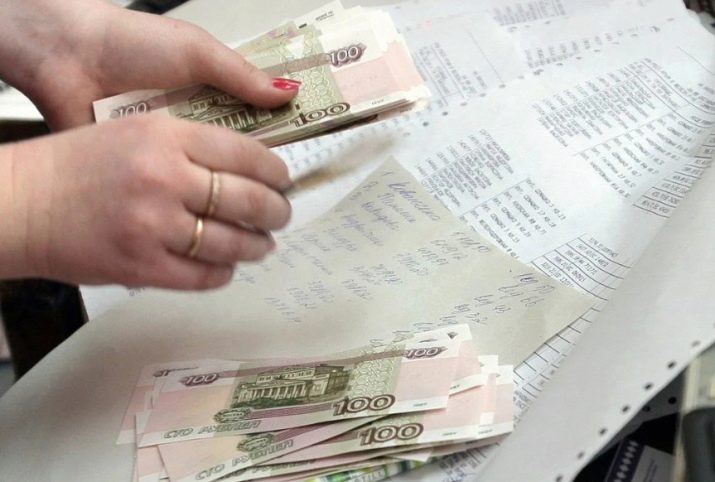
Responsibilities
The complexity of the work of a tool-maker, its quality, accuracy and order determines the level of skill of specialists. The higher the category, the more time-consuming will be the work to which a specialist can be admitted. The level of skill of the toolmaker is determined in accordance with the assigned categories prescribed in the ECTS. In general, the job description of a qualified specialist includes the following duties:
- processing of workpieces with a precision level of 12-14 qualities;
- assembly and repair of tools and devices for further hardening of the tool;
- manufacturing and bringing to the required parameters thermally untreated billets for hardening with a degree of accuracy of 12 qualifications;
- threading using taps and dies, as well as its alignment with calibers;
- creation and subsequent plumbing of tools, as well as mechanisms of medium complexity;
- practical use of specialized equipment and technological templates.
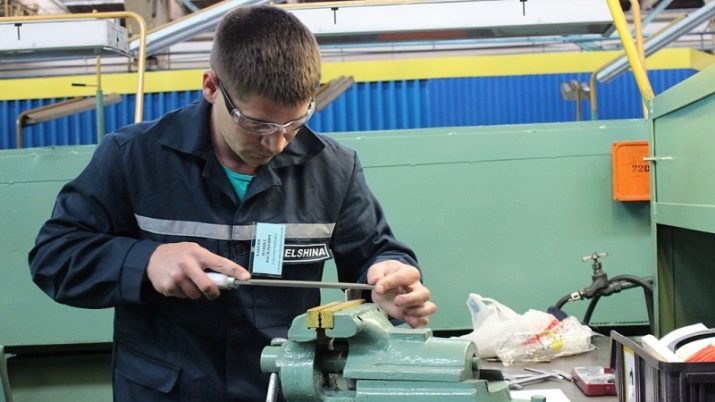
Knowledge and skills
In order to achieve all the tasks set, a competent toolmaker must have perfect mastery of work skills in various fields. Strong knowledge is required from him:
- about basic geometric as well as trigonometric dependencies;
- on the theory of engineering drawing;
- on the arrangement of operated metalworking machines, as well as equipment for lapping and lapping types;
- on operating conditions for lapping materials;
- about the physical, chemical and technical features of steel of various grades;
- about instrumentation, their design characteristics and operating rules;
- the dependence of the accuracy of the measurements on the level of heating of the part;
- on methods of heat treatment of all types of steel;
- allowances in the process of fine-tuning, taking into account the parameters of changes in the properties of the metal during thermal exposure.
The toolmaker must have a technical mindset. He should be able to compose and decode drawing symbols well, to represent future products in volume. They require spatial thinking skills, an understanding of the specifics of the main working tools, as well as the economic feasibility of using certain processing methods.
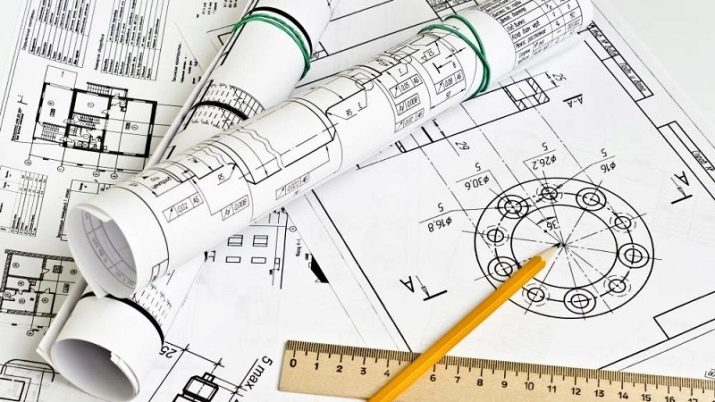
When performing markup, he will need strong knowledge of geometry. This person should have an understanding of the methodology for marking planes and features of surface curvature. The presence of a volumetric as well as linear eye is important.
For fine-tuning or control measurements are required not only physical effort, but also high sensitivity of the hands, good coordination: the toolmaker must quickly grasp the parameters of the change in pressure and fineness of metal resistance, direction of movement, as well as their working dosage and application force.This will avoid overly frequent measurements and significantly save the working time of specialists, as well as increase his level of professional skill.
Since tool refinement of equipment is considered one of the most time-consuming and lengthy operations, a locksmith will need steady attention and patience. Work in this position requires the presence of certain personal characteristics. These include:
- curiosity;
- wide technical outlook;
- high level of responsibility;
- scrupulousness;
- hard work;
- predisposition to perform monotonous work.
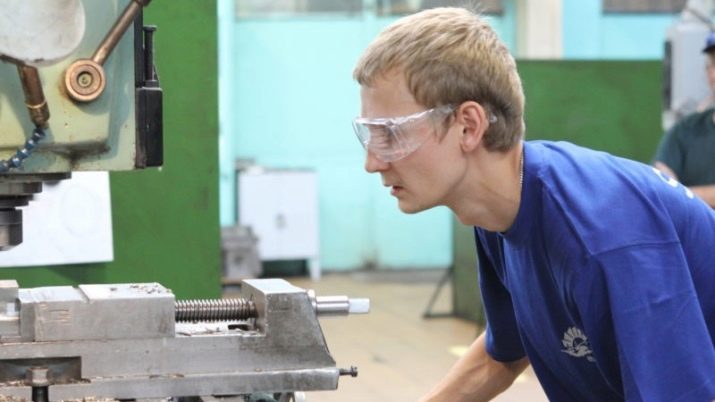
Training
To find a job as a tool maker, a specialized technical education is required. However, getting it is not so difficult, since this specialty is represented in almost all vocational schools, they are recruited on the basis of 9 or 11 classes. The training program includes both special and basic disciplines, much attention is paid to industrial practice. The so-called “targeted training” is widespread - in this case, students of secondary secondary education institutions were invited directly to the plant with subsequent employment if they had practice at it.
Another way to qualify a toolmaker are courses that are conducted by the UOC. As a rule, they take much less time than obtaining diplomas from colleges and technical schools, however, they are also more concise in time. That is why most often they are addressed by people who already have some skills in the technical field as a worker.
Above all, training received directly at a manufacturing enterprise is appreciated. when an experienced worker acts as a teacher and allows his student to master all the intricacies of the specialty in practice. However, in this case, the duration of training and obtaining the entire necessary range of skills will depend directly on the specialist and the employment of his curator. The position of a toolmaker offers career opportunities, they are associated with increasing the level of professional category. Within the framework of the specialty, several qualification categories are distinguished:
- 2 category - the activity is carried out under the supervision of an experienced specialist, only the simplest jobs are independently performed;
- 3 category - the ability to work independently with equipment of the third level of complexity;
- 4th category - allows for the repair and production of technological devices;
- 5th category - provides for all the functionality listed above, and also makes it possible to carry out the adjustment of complicated technological equipment;
- 6th category - involves working with unique equipment;
- 7th category - includes the installation of unique equipment using special equipment;
- 8th category - involves working with experimental prototypes.
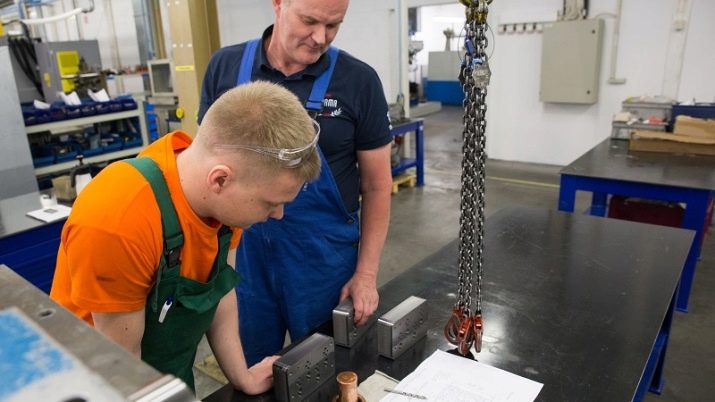
Where does it work?
Toolmaker has the opportunity to find a job at any manufacturing enterprise in the field of machine and instrument engineering. This employee is personally responsible for the accurate and timely fulfillment of all the goals and objectives set for him. At the same time, the ion may require its management to provide it with the necessary conditions for effective activity.
Only a tool maker can start independent activity after undergoing mandatory training on labor protection and occupational safety rules, electrical safety, fire safety, as well as first aid. It should be noted that during the performance of labor duties, these briefings will be regularly repeated in accordance with the plan established at the enterprise. In addition, any toolmaker must undergo a medical examination every year and confirm at least once every 3 years the level of his qualifications.
In their work, each tool maker is based on the following regulations:
- approved job description;
- adopted labor protection rules;
- fire safety regulations;
- electrical safety regulations.
In the process of performing the work, the tool maker must use protective equipment (gloves and glasses), as well as wear protective clothing.
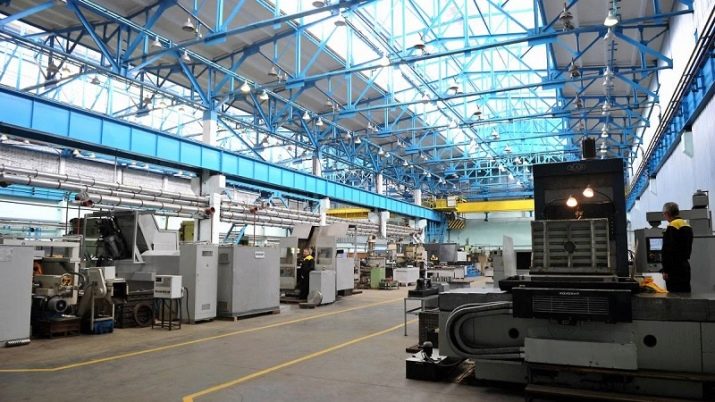