Home-made furniture is a matter of pride, a chance to learn furniture business, craft. If you like to create, craft household items, then home-made furniture is not only your hobby and means of self-realization, but also a significant profitable article. Unless, of course, you quickly master the whole process and prove yourself in the best possible way.
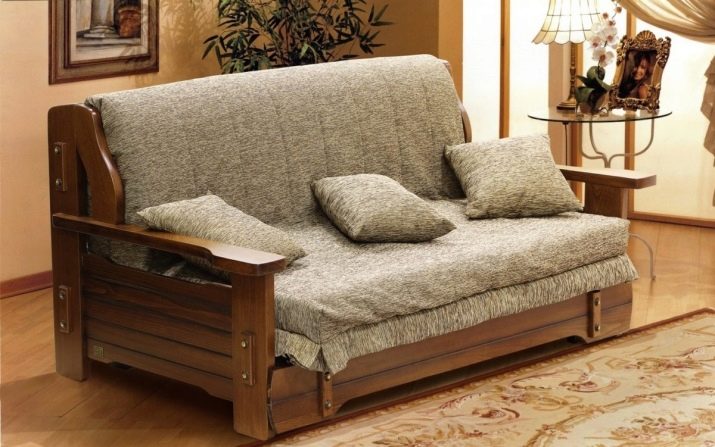
Features of homemade furniture
Homemade furniture has the following advantages.
- The ability to give the desired look, which has no analogues in any store of finished furniture items. Do you want the sides of your sofa to resemble a jam cake in which sections of the pattern made of dough are filled with filling? You can create exactly the same relief by sawing and turning the layers of plywood. At the same time, the outer layer itself is painted with a colorless varnish - and the recesses formed by the second board lying under the first are painted with dark brown or red-brown varnish.
- Use only natural wood. Don't like plywood? Buy a board - the right amount of pieces of a certain length, width and thickness - and do whatever you like.
- An opportunity to use the most high-quality accessories from old sofas, beds, armchairs. Are there only chipboard products in the store? Porch neighbors threw away old furniture, which has solid boards, sheets of plywood? Or maybe someone threw out the old Soviet door with a jamb? Know how to assemble furniture for your own reasons, even without a plan? Gather these pieces of wood, planks and make a sofa, bed, chair-bed in a classic manner. And then refine, create your own design.
- Want to excel? For example, can you burn wood? Draw a picture with a soldering iron or a sunbeam in the summer, caught in the focus of a magnifier. And cover your “graffiti” with furniture lacquer, painting the entire board on which they painted.
- Furniture, assembled with your own hands from existing materials, is several times cheaper than finished. You can get a bigger margin in price if you have a lot of second-hand but well-preserved wood extracted from old furniture. An alternative may be cast wood-epoxy-plastic material - cast composite, from which moisture-proof interior doors are made. If you come across a door that has served its purpose - subject to the integrity of the canvas, such material will also fit on a sofa or bed
- The most valuable thing is experience.. Even making ready-made schemes and sketches, painted step by step, a completely “green” beginner will sooner or later learn to make masterpieces that are not inferior in quality to the purchased elite furniture.
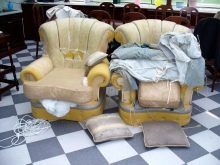
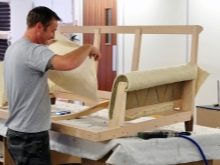
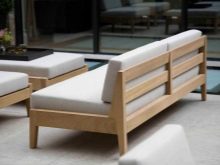
The disadvantages are as follows.
- At first, a novice, until he honors a series of actions to automatism, will spend more time making furniture.
- This lesson is very labor-intensive and resource-consuming, it takes up a lot of personal time.
If a person has learned this business and decided to register as an individual entrepreneur in order to make good money, then he will need to regularly bring in new materials and structural elements, keep his warehouse, work in a continuous stream of orders, sometimes update worn out consumables for tools.
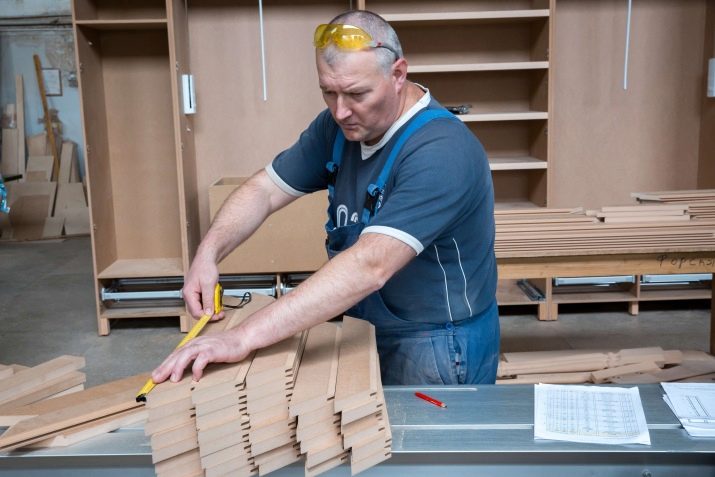
What can be made of?
Do-it-yourself sofa is made of the following elements and designs.
- From car seats. Seats are bought in the car market, in a specialized automobile hypermarket or car shop at the service station. The rear seats from any passenger car will do - a prefabricated kit, which can accommodate 3 or even 4 people in the back. Check which car models are 6- and 7-seater and buy a prefabricated seat for one of these car models. You can use the seats for minibuses - brands "RAF", "GAZelle", "Ford" and other passenger vans. They are arranged in a row - the rear has 4 seats. The main thing is that their sidewalls do not dig into the person lying on them, and also lean back. In theory, any seat with a reclining back will do.
- Made of wood. Any sofa design, dozens of variations to help you. But several types - “book”, “corner”, sofa, frame, frameless - there are still. Any frame is made of wood or chipboard.
- From metals and their alloys. Any aluminum or steel profile will do. If you are a fan of furniture with a purely metal frame, then even a thick (60 * 25 mm) reinforced cornice aluminum profile, stainless steel corners will do. However, thick steel (from 4 mm) in a corner, tee or P-profile, as well as in pipes, will result in a sofa welded from ordinary steel pipes and profiles weighing 300 kilograms or more. It will be possible to move it unless ten times, and for the removal, transfer from the house or building of a non-separable sofa will require the help of at least 20 people. Such a sofa over time sells a regular floor, due to which the design is suitable only for a yard or an arbor, but not for a house. Particularly distinguished units boiled sofas even from old rails taken off an abandoned railway gauge. As a result, such a design weighed as a Moskvich-412 - a ton or more.
- Of two mattresses - except for inflatable ones. But mattresses do not hang in the air, and are also installed on a base - trellised with legs, boxed, sliding, folding, etc. In the simplest case, the base is a door leaf, to which, instead of a jamb / platband, the second one is screwed on hinges. Folding legs are screwed to both doors serving as sofas of the sofa (hinged with a lock).Additional spring-latch mechanisms are installed from the ends, which do not allow the sofa to open - if it does not stand against the wall, but in the middle of the room. If the doors are sold only complete with door frames, then the spare parts of the latter go to sofa legs, beams, etc.
- From rattan. This is a woven stripes texture. It resembles a 200 times enlarged fabric texture, in which the threads are woven in the same way - perpendicularly. They alternately follow each other. The strips can be fabric, plastic, rubber, etc. Rattan can be woven from anything - cut into strips of linoleum, an electric wire coil (or a removed protective sheath of old cables), a cord, a rope, or even a thin rope. Rattan is an alternative to upholstery. That is how earlier baskets, hats, etc. were woven from the branches of plants.
- From tires. Car tires - the base on which to lay boards or upholstery with filler, forming the flooring and backrests. Tires from passenger cars are not hard enough. Here you need tires from a truck, tractor or special equipment (truck crane, bulldozer, rear wheels of a tractor, etc.). This option is perfect for a garage or loft living room.
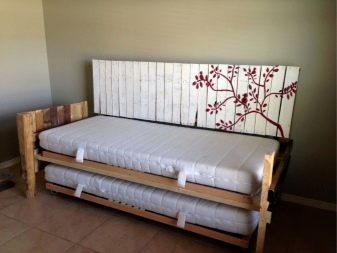
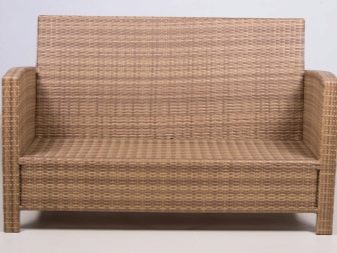
Having decided what you will make the sofa from, look for a diagram indicating how your product will come to life.
Manufacturing schemes
Any drawing of a sofa made by yourself, immediately reports on the type of design.
It can be U-shaped, modular, in the form of a sofa bed (folding), in the style of a bay window (parallelepiped or polyhedron) or semicircular. The latter includes, for example, a tire structure, where the sidewalls are made of their halves.
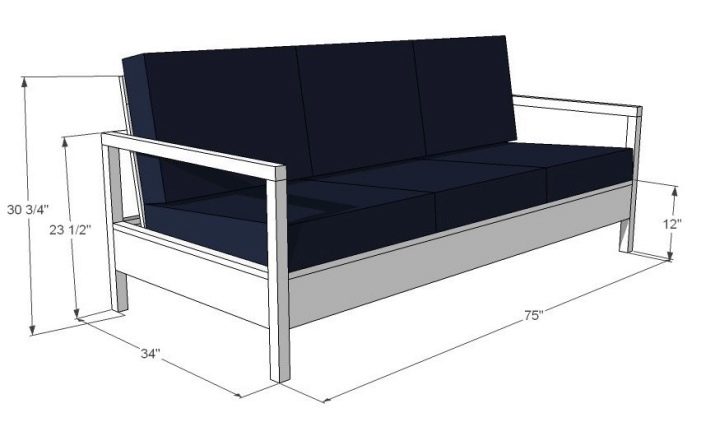
Wireframe
To make a frame sofa at home, you need the following materials: wide boards, bars, battens, screws, epoxy (or carpentry) glue, dowels, putty and sofa cushions (or a sofa). Of the tools - a miter saw, an electric drill, a grinder with a set of grinding disks, a screwdriver, a pair of dowels for dowels and self-tapping screws, clamps of different sizes, a conductor for angular drilling, a spatula, smooth fabric, a square, a pencil, a tape measure "meter".
To prepare the elements of the sofa, do the following.
- Divide the boards into pieces of the desired length. So, 6 segments are needed for setting the dimensions of the base of the sofa with shelves.
- From the bars, make segments of the lamella base. Two sets are needed - for the seat and back.
- Scrape all parts with a 220 grit wheel.
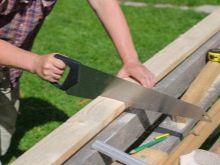
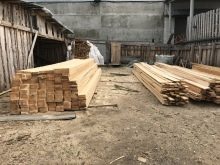
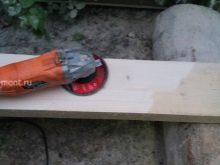
For staining, all external parts, their sides should be especially smooth. To assemble the support frame, do the following.
- Use the dowel-free method of joining parts. Using a jig, drill holes at the desired angle. For dowels, select the correct drill bit and make sure that the dowel enters the groove with some effort.
- Fasten the parts of the supporting base with the shelves using self-tapping screws and glue. Before the epoxy adhesive dries and hardens, do not remove retaining clamps from the structure.
- Insert the upper structure into the base with dowels.
- Combine all the resulting parts of the structure on a flat floor and attach them to each other with glue and screws.
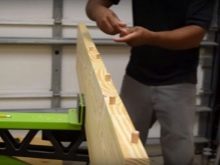
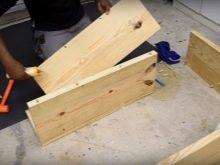
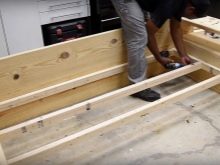
After the epoxy hardens, proceed to puttying the structure.
- Putty holes remaining after screwing in the screws.
- After the putty dries, “sand” the places where it hardened.
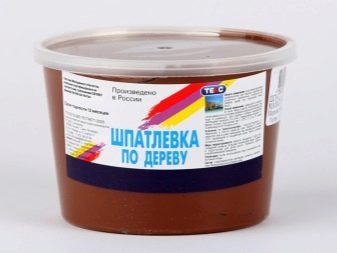
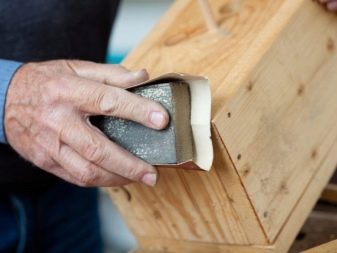
After leveling, apply a special oil that protects the tree from moisture with a brush.
To make a bearing support under the lamellas, do the following.
- Lock all parts using temporary joining using trimmed boards.
- Lock the lamellas on the base, positioning them so that they enter when you move the sofa into each other.
- Fix the narrow board with the lamellas using the same epoxy.
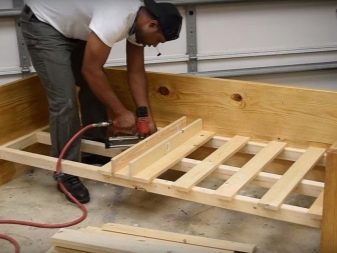
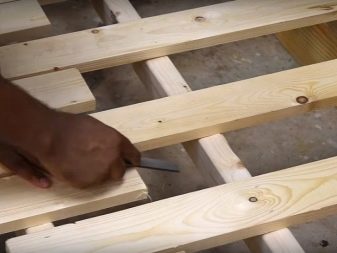
To make a sliding structure, do the following.
- Secure the wide front board for a while with the three stops.
- Put the frame on these stops so that the same board is immobilized for the duration of further actions.
- Attach the remaining lamellas so that a small gap remains between them.
- Check how the retractable structure slides and extends. For ease, screw the rollers in movable places - the sofa will be easier to push apart.
After assembling the main parts, position the sofa and pillows. The sofa is almost assembled.
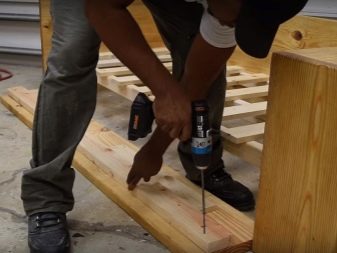
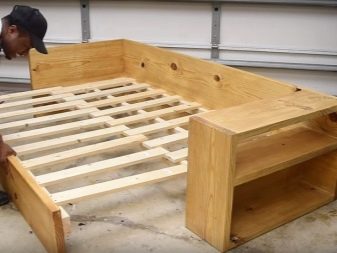
Frameless
Need: foam and coarse, dense fabric for lining, glue, threads and needles, chalk, zippers and flock. Of the tools - a sewing machine and scissors. Do the following.
- Cut pieces of 160 * 90 * 4 cm from the foam under the base, 160 * 60 * 4 cm under the seat.
- Cut also parts: 160 * 30 * 4 and 160 * 50 * 4 under the back.
- For pillows, cut 6 sheets of foam rubber - pillows will gain a height of half a meter. Glue the foam layers and sheathe them with covering material.
- Sew upholstery from the flock, cutting the fabric under the pillows.
- Install a zipper on each of the pillows on one side.
- Assemble a sofa. Frameless model is ready.
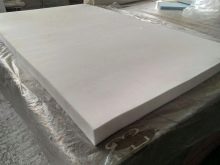
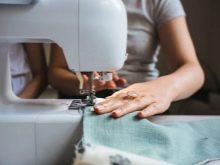
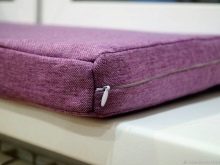
Corner with retractable mechanism
A retractable corner sofa allows you to place an additional storage inside - under the seat. Of the tools in its manufacture you will need: an electric jigsaw, a grinder with a set of grinding disks, an electric drill, a furniture stapler, a sewing machine, a screwdriver, plywood or a board with a thickness of at least 12 mm, wooden blocks with a cut of 50 * 30, 5 mm plywood, fiberboard sheets, fabric for upholstery, self-tapping screws, epoxy adhesive, steel furniture corners, foam or felt, spring unit, ready-made legs for sofas.
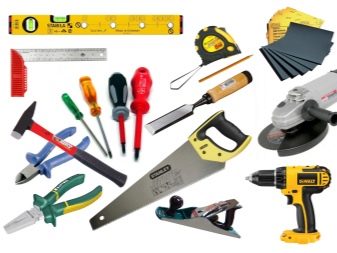
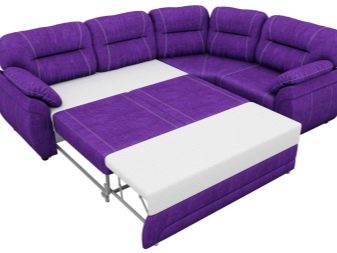
To make, do the following.
- Cut the necessary parts and connect them with the corners on the screws.
- Close the bottom of the structure with plywood or fiberboard.
- From above, also close the box with plywood, putting the hinges.
- Assemble the backrest and attach it to the front structure.
- Attach a fiberboard back to cover the back of the back. Use a stapler to pull the fabric over it.
- Glue or attach a layer of foam rubber with stapler pins.
- Establish a spring block on a seat, cover it with foam rubber.
Cover the seat with an outer fabric cover to cover the inside of the seat. Now you can make and install boxes under the seat by attaching handles to them.
Corner sofa with drawers assembled.
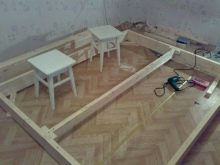
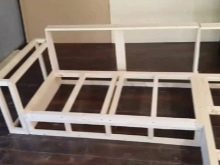
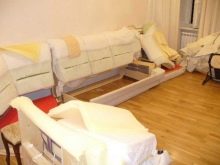
Sofa book
In addition to wooden boards and plywood, buy transforming devices.
- Saw boards and plywood into the necessary elements and connect them using epoxy and screws. Wait for all structures to gain strength.
- The result is a set: seat, back, drawers, armrests. Start assembling the sofa from the seat. Install "transformers."
- Put the back and set the drawers.
Perform upholstery - install foam and wash the fabric.
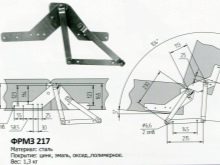
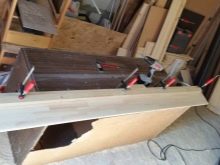
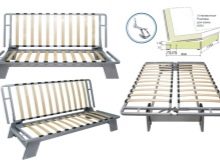
Dressing
Start installing upholstery with foam. Glue the foam strips to the armrests, back and seat. Use a fabric resistant to abrasion and wear so that it does not fray in a short time, for example, in a year. Choose material that is easy to clean and clean in case of accidental contamination. The sofa, which can get splashed, for example, fly into the gazebo with oblique rain, it is worthwhile to protect with a water-repellent fabric with impenetrable impregnation - like the one used on waterproof jeans and windbreakers.
If the sofa is in a place where direct sunlight is present - the matter should not fade, crumble from ultraviolet radiation over time.
Pay special attention to the color scheme: it should harmonize with the design of the room in which this sofa is installed.
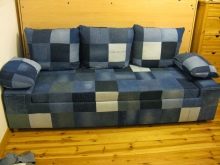
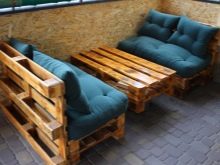
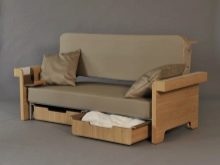
Properly assembled and decorated with high-quality upholstery, the sofa will organically fit into the interior of any room. It can be put both in the living room and in any of the bedrooms.Paying special attention to its manufacture, approaching its creation with all care, you will receive a piece of furniture that not only you but your children and grandchildren will be proud of.
A master class on making a sofa (in 2 parts) can be found in the video below.