Drivers and teachers of schools, paramedics and divers, slingers and border guards - such work is more or less understood by most people. But there are areas of activity much more difficult to understand, far from everyday practice and simple comprehension. Therefore, it is necessary to find out, for example, everything about the profession compressor operator - then the choice of this specialization will be fully realized.
Features
Giving a general description to the compressor unit operator, it should immediately be noted that manipulations with various types of process compressors do not necessarily imply a fixed workplace. Indeed, many compressors are of a mobile type, that is, they are installed on vehicles, and not on a construction site or industrial enterprise. Anyway, the specialist is responsible for the entire cycle of the equipment. After all, the slightest failure is enough for the technological operation to not be performed, and the company suffered serious material and reputation losses.
This profession, like any other, has its positive and negative sides. In our country, there are a lot of technological compressors. But because the likelihood of being unemployed is relatively small. Career prospects are also quite impressive.
But you must understand that the compressor driver is always a risk. And the level of responsibility is quite high, and in case of an error, blaming the blame on someone else will fail.
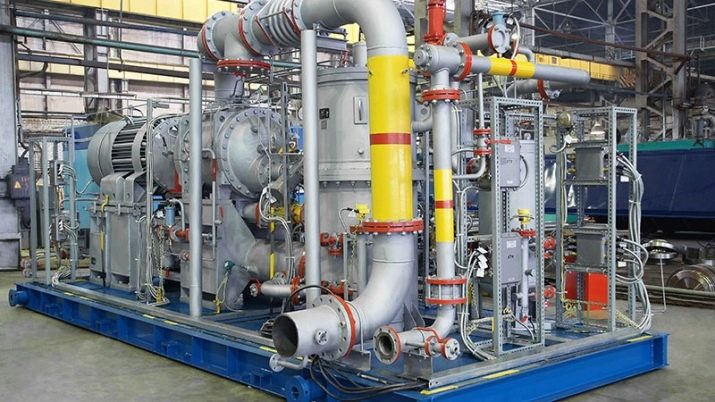
Responsibilities
It is most correct to characterize the duties of this professional according to ECTS. He will:
- Serve the main components of the technological chain;
- Serve connection nodes and oil distribution systems;
- monitor the correct consumption of water, antifreeze and other process fluids;
- start and stop the units by order of the management or as necessary;
- perform simple adjustment work on the entrusted area;
- Serve individual process compressors
- to regulate the operating modes of units in production;
- promptly switch low-voltage electrical installations to the required modes;
- find and fix simple malfunctions in the equipment used;
- maintain repair forms.
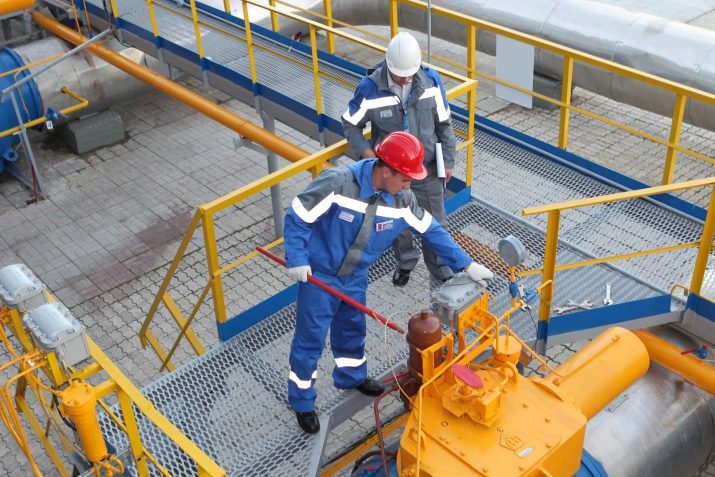
The most qualified compressor unit drivers:
- serve compressor stations as a whole, control panels;
- Engaged in general workshop systems for the handling of compressed substances;
- bring technological systems to repair;
- establish compressors, their drives and apparatuses;
- work with auxiliary equipment in the workshop;
- coordinate the work of lower class drivers.
It is worth noting a number of prohibitions that compressor unit drivers must strictly comply with. So, they are allowed to work only in tight clothes that are not fluttering and fully buttoned. In rooms with compressor installations there should be no extraneous equipment and apparatus.
During operation of the compressors, it is necessary to carefully monitor their operation and all sounds. Having noticed a leak of oil or water, the specialist must not only clean them, but also immediately identify the cause of the leak, and then eliminate it.
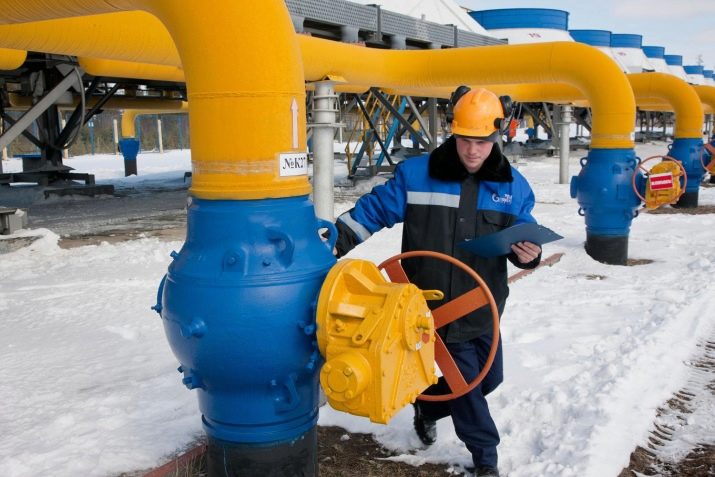
Knowledge and skills by rank
Engineer compressor units 4 categories - This is already a fairly serious specialist. He must know how the compressors and their drives are arranged, how the whole system as a whole is controlled, and what kind of emergency situations can arise in operation. We will have to study the basic control devices and protection systems of technological equipment, personnel. You will need to know the characteristic signs of the abnormal development of events and ways to address them. If the pumping system drive is powered by electric current, there is nothing for the person in the workshop who does not have group III for electrical safety.
Higher demands are made, naturally, to machinists of the 5th category. Those should already know not only the general structure of the entrusted technology, but also the circuit diagrams of control automation, the rules for its use. It will be necessary to study the general structure and the main principles of the operation of instrumentation, sensors included in the control system. After all, all this will have to be repaired and special documentation drawn up, so that later the involved professionals can figure out the situation. If the systems are electrified, you will have to get the IV group of electrical approval.
But the most stringent requirements await applicants 6th category in the profession. Such compressor unit drivers must know:
- how gas is transported (technology basics);
- layout of pipelines in the workshop and in the enterprise as a whole;
- rules for the use of automatic control systems;
- technical specifications and practical rules for all types of repair and adjustment of production apparatuses;
- basic approaches to repair drives, valves;
- technological subtleties of gas lift and cycling process.
Still worth mentioning about such skills:
- readiness to lubricate compressor and associated equipment;
- monitoring the quality of safety systems;
- timely detection of signs of a critical situation;
- knowledge of working pressures, temperatures and other parameters at each link of the technological chain;
- ability to detect overheating in time and eliminate it;
- brands of lubricants, their features and application nuances.
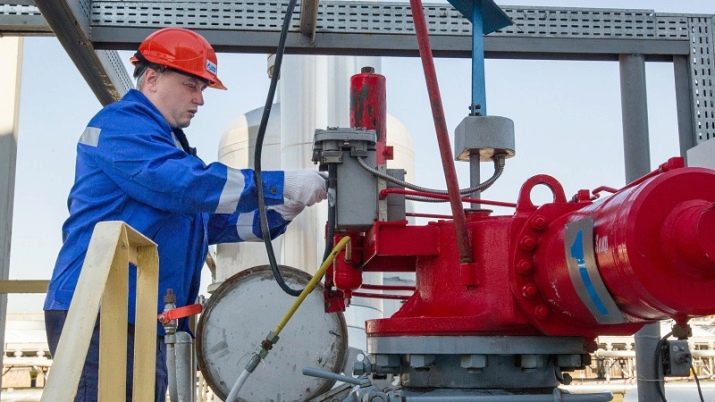
Training
In order to become a compressor unit engineer, it is necessary to obtain a secondary specialized education in the corresponding profile. Such training is conducted in a variety of educational institutions in our country. But first of all, we can recommend:
- Moscow College of Technology;
- 33rd Moscow Food College;
- Polytechnic Kazan College;
- Volga College of Construction and Energy;
- Omsk College of Meat and Dairy Industry;
- Engineering College of Krasnodar;
- Industrial College of Volgograd.
The same profession is taught in individual higher education institutions. So, such training is being conducted at the faculty of secondary education Research Technological University in Kazan. And in Kant Baltic University of Secondary Vocational Education. And there are:
- Marine Technological College at the Admiral Nevelsky University of Vladivostok;
- Polytechnic College at the University named after Peter I in St. Petersburg;
- Petersburg College of Fisheries (this time - a representative office of the Kaliningrad Technical University);
- multidisciplinary college at Tsogu.
If these educational institutions do not seem enough, then you can still consider:
- Ufa College of Industrial Technology;
- College of Energy and Communications in Volgograd;
- Petrochemical College named after Lushnikov (Kazan);
- educational complex named after Talalikhin (Moscow);
- College of Economics and Technology (Yekaterinburg);
- Vladivostok College of Fisheries at the Far Eastern Technical University of Fisheries.
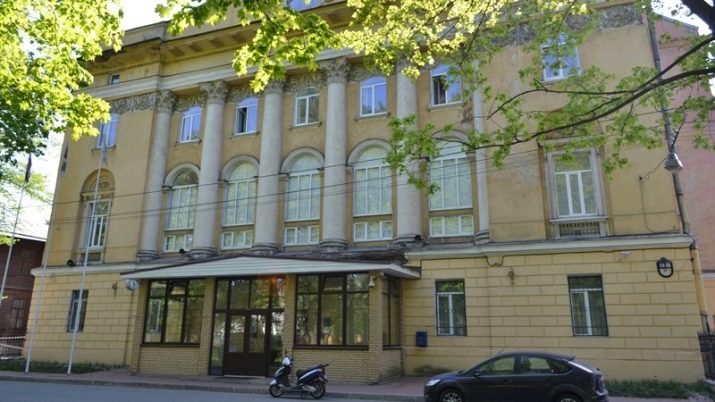
Workplace
Since the compressor unit operator works with complex long-range processing equipment (including air lines), he has to constantly move around. When certifying a work site, take into account:
- biological hazard level;
- the number of pathogenic microorganisms;
- concentration of hazardous organic substances;
- air saturation with dust and aerosols;
- noise level;
- the intensity of exposure to ultrasound and infrasound;
- total and local vibration;
- electromagnetic fields;
- radiation without an ionizing effect;
- ionizing radiation;
- temperature, pressure and humidity;
- the speed of air movement in the room;
- level of thermal radiation;
- illumination.
Industry standards require compressor units to wear protective clothing. It is mandatory even in cases where the certification of the workplace has not revealed any deviations from the established requirements. Safety regulations require that no one under the age of 18 be allowed to do this work. To protect against potentially dangerous factors, use:
- noise absorption means;
- dielectric gloves;
- dielectric shoes;
- overalls or cotton suits;
- combined mittens.
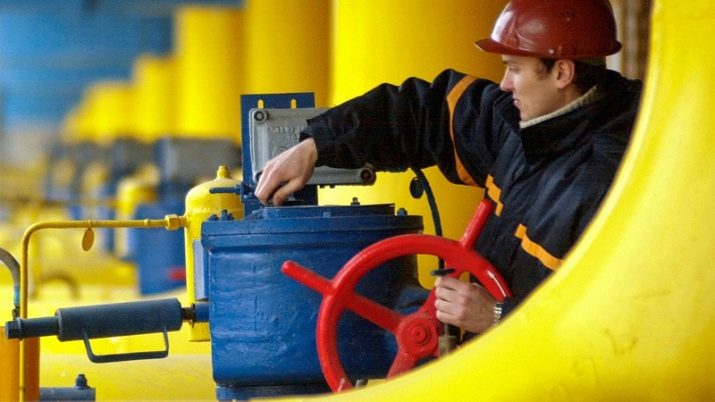