Chiptop worktops today can no longer be considered the most popular, and yet they have a certain number of fans. At least, many manufacturers still do not refuse to produce products from material that is so often criticized by certain segments of the population. This means that some demand remains, therefore, it is worth getting to know the worktops from particleboard closer.
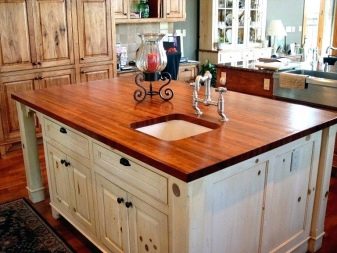
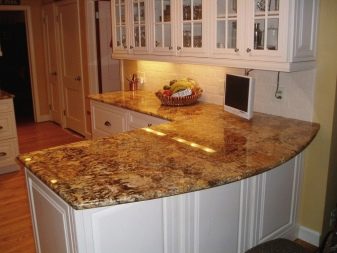
Advantages and disadvantages
Just a couple of decades ago, a kitchen worktop made of chipboard was a mass phenomenon, but today it has been largely replaced by more modern materials. The fact that the particle board has still not disappeared completely indicates the presence of certain advantages of its use, which should be considered carefully.
- Low cost. We can safely say that this is the main selection criterion, since there are simply no other cheaper alternatives.
- A variety of colors and textures. Particleboard kitchen worktops can look completely different since the material involves simple processing, it can be painted and even contain a complex print.
- Resistance to burnout. A pigment that gives a color to a monophonic plate can be incorporated into the substance at the manufacturing stage, because ultraviolet rays are not scary to the product.
- Relevance in the kitchen. Immediately make a reservation that all these advantages are relative, however, a particleboard made of chipboard can tolerate high temperatures and mechanical stress, and it is also practically indifferent to the activity of food acids.
- Laminate coating. In most cases, in the kitchen, a laminated version of the stove is used, which has no pores, and therefore does not lend itself to destruction by moisture and does not absorb dirt.
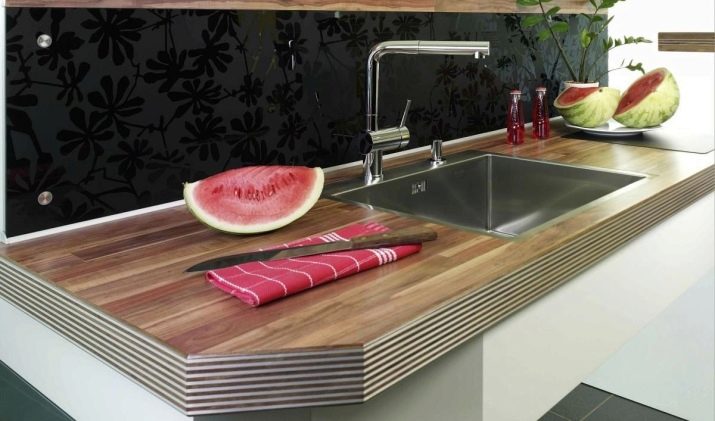
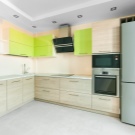
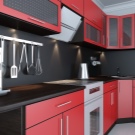
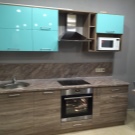
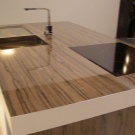
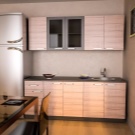
Despite all the above qualities, it is indisputable that most alternative materials are superior to particle boards in terms of basic characteristics, which is why the particle board has lost its superiority to competitors. The obvious disadvantages include a number of features of particleboard.
- Formaldehyde in the composition. In recent decades, humanity has been increasingly attentive to toxins, even in their own home. Particleboard contains a lot of extraneous "chemistry" that can be released into the air. Manufacturers claim that they have reduced the amount of toxic glue and resins in the composition, and lamination from all sides prevents secretions, but you yourself must understand that the risk does not go away.
- Swelling from moisture. If water finds an opportunity to get through a layer of laminate to a wood-chip core, it will surely cause the latter to swell. The consequences will be the deformation and loss of an attractive appearance or even the convenience of using the table.
- The doubtful reliability of the laminate. The two points mentioned above show that without a complete lamination of chipboard, the material is rather dubious. In the meantime, damaging the laminating layer is quite easy - with a knife, alkali or concentrated acids.
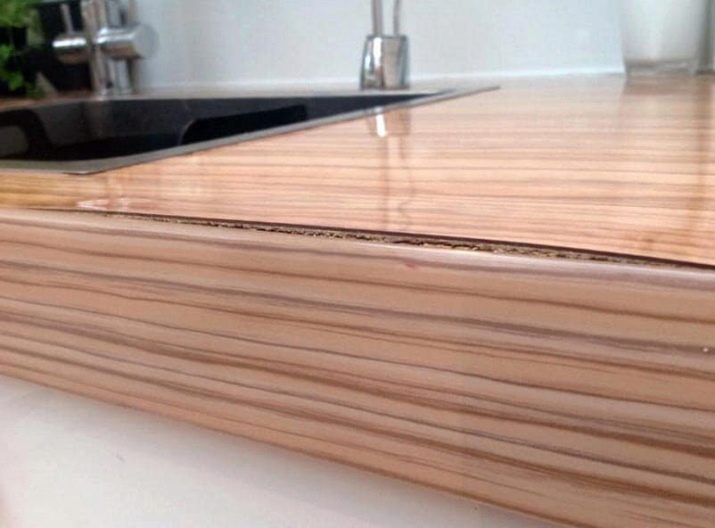
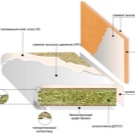
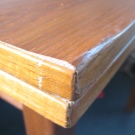
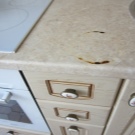
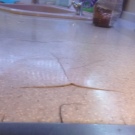
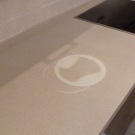
What is postforming?
Given the aforementioned dubious qualities of the board, which it has in unprotected form, the production of countertops usually directly assumes that the finished product as its outer layer will have some kind of “wrapper” that protects too fragile and potentially dangerous pressed chips. At the same time, most bona fide manufacturers prefer to optimize the operation of the slab thanks to a method called postforming.
Its essence is that plastic lamination occurs at high temperatures and with the participation of a special press. The plastic coating layer acquires smooth bends, so the finished countertop will not have sharp corners or cuts - it will become smooth and sloping on all sides. This form significantly minimizes the risk of injury, and also contributes to additional protection of the core from moisture.
There are two main types of postforming boards. The simplest is called the L-type, in this case, the plastic covers the chipboard on one side and at the end. The so-called U-type is even more effective when the plastic layer “hugs” the countertop from two sides.
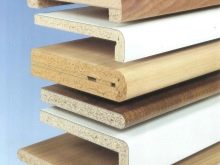
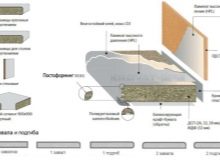
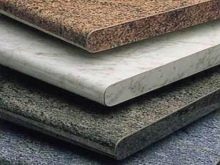
Types of Coatings
Laminated chipboards for additional protection against negative external influences and to improve the appearance of the outside are coated with different materials, which are called the general term “laminate” for convenience only. The protected sheet is briefly called chipboard. Its specific characteristics depend on which version of the laminate was used.
Most often, four basic materials are used, each of which is worth considering separately.
- Melamine foil. In fact, this is kraft paper, which is impregnated with a special melamine resin for greater reliability. The thickness of the protective layer is even slightly less than half a millimeter, but such a coating can have the most unexpected colors and patterns, and therefore is in great demand.
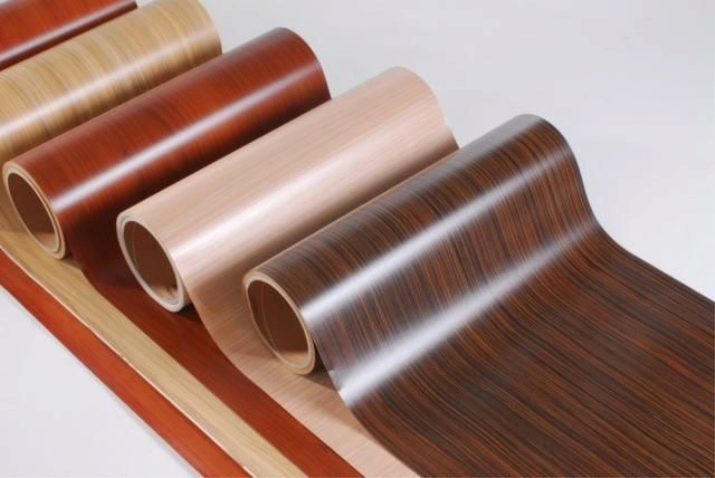
- Plastic. One of the most popular laminate options, which at a relatively low price provides sufficient protection parameters for chipboard. There are two types of plastic coating - high pressure sheet and continuous pressure roll. By most criteria, both options are identical to each other, but differ mainly in thickness - the second is much thinner than the first (0.15-1.5 mm versus 0.5-6 mm).
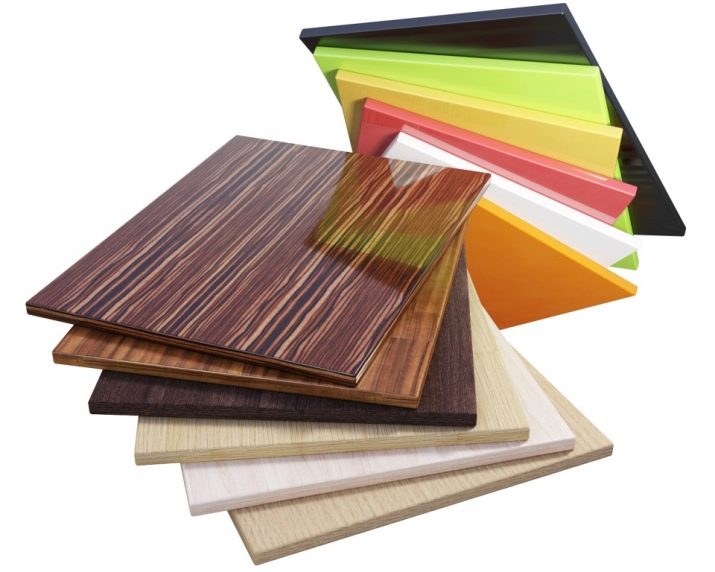
- Veneer. This option of lamination could be appreciated very highly if it were as practical as it is beautiful.The veneer is laid out on top of the chipboard, everything is varnished on top, so the finished countertop seems to be a natural solid wood and looks simply amazing. At the same time, the product does not differ in moisture resistance at all, and it is also very easy to scratch it, because in kitchens this finishing option is not often found.
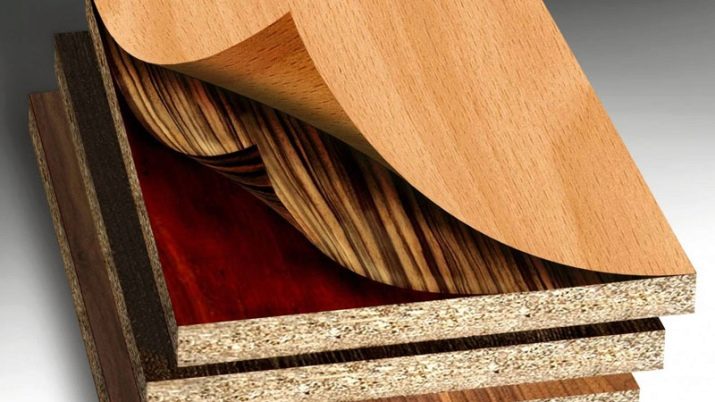
- Stainless steel. Perhaps it is not entirely correct to call such a material a laminate, and yet they can be trimmed with chipboard worktops. With the right approach to design, this may look pretty pretty, in addition, it is also very practical, but such a solution will cost the customer quite expensive, because the option is usually only appropriate in public places.
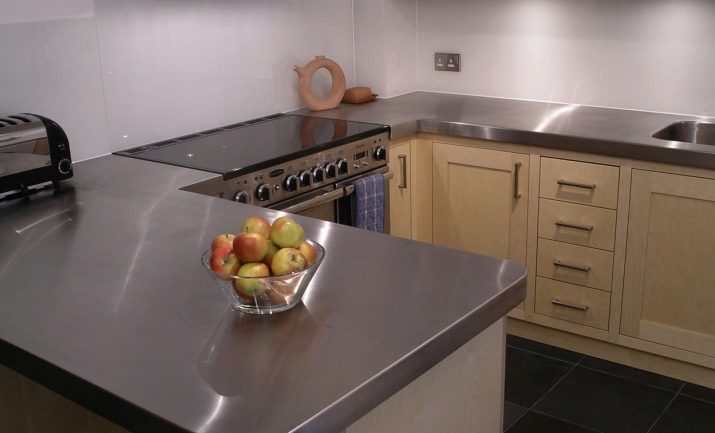
Dimensions
Worktops made of any material can be either finished, manufactured by the manufacturer in standard sizes and sold in the construction hypermarket, or individual - these are made to order, and therefore can have any shape and size. Separate production of a single instance, of course, costs more, and since particleboards are often chosen precisely because of their low cost, it is clear that individual orders from this material are rare.
The thickness of the countertop is one of the most important characteristics, because for a relatively brittle (compared to the same stainless steel, MDF or ceramic) material, it gives a certain margin of safety. Standards of 28 and 60 mm are quite common, but the most common is considered to be a thickness of 38 mm.
In principle, if some outstanding loads are not expected, you can use a plate of any thickness from among those that are presented in the nearest store.
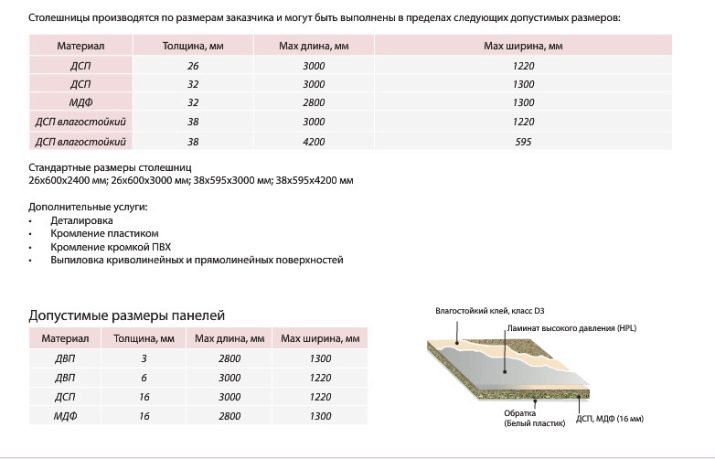
The width of the tabletop made of chipboard is even more varied - the plate can have both 400 mm wide and 1200 mm. Postforming inevitably adds a centimeter or two to the length of the countertop, so you need to clarify whether its protrusion is included in the declared indicator or not. Choose the width of the product so that the owners can easily reach the far edge of the countertop located against the wall, and therefore most often choose models with a width of 600 mm.
The advantage of chipboard worktops is that the range includes models of different lengths - from 2450 to 4100 mm. This is especially important, given the fact that trimming the product is undesirable - this will violate the protective circuit of the laminate.
Due to the variety of sizes, you can choose a stove that most accurately fits into the dimensions of your kitchen.
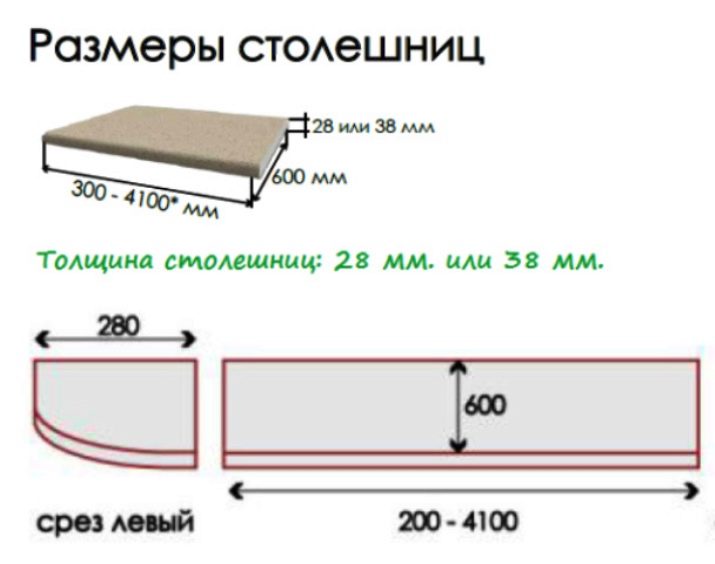
Color schemes
Particularity of chipboard is that in the production process pigment of any color can be mixed with pressed chips, so the finished product does not even have to be painted - it will already have a certain shade at the exit from the conveyor. Most often in production they are guided by the most popular colors, which include black, white and shades of wood. The advantage of this color is that it does not fade.
If necessary, chipboard, like any other material, can be painted already from the outside, including by applying a print or pattern to its surface. In this case, it is usually necessary to decorate not so much the chipboard itself as the outer layer of plastic or another laminate. Manufacturers usually do not offer intricate design options, the height of the complexity for them is some kind of pattern.
Wanting to apply something more original to the stove, the consumer will have to order an individual model release.
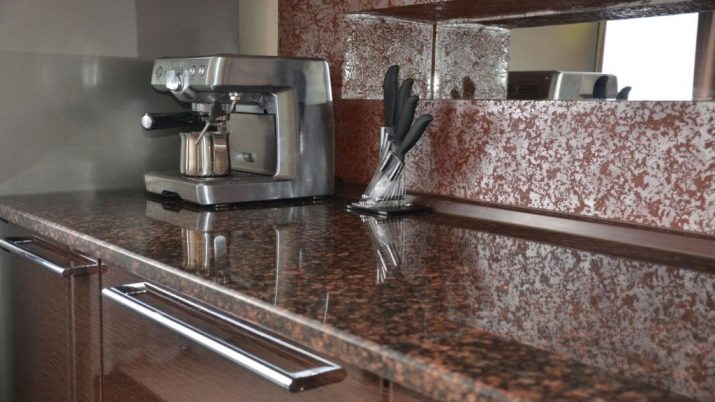
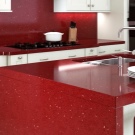
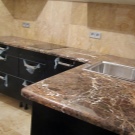
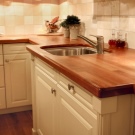
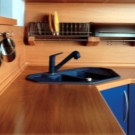
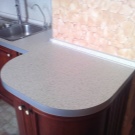
How to choose?
Regardless of whether you need a countertop for a table or as a cover for a kitchen set, the first thing you should pay attention to is dimensions. The length and width of the product are determined not so much by your own wishes, as by the dimensions of the kitchen, which usually puts its owner in a tight framework.
As for thickness, then it is usually chosen arbitrarily, unless you are trying to imitate something. For instance, Particleboard, similar in appearance to natural stone, simply cannot be too thin - from this, it will seem implausible and ruin the interior.
It is important to choose the right decor countertops, so that it competently combines with the color scheme of the room, and with the style of its design.
If a chipboard imitates another material, then it should be appropriate: “metal” will fit into the kitchen in a high-tech style, and “wood” is perfectly combined with ethnic design.
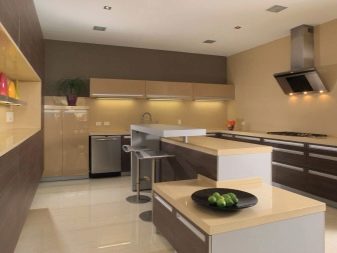
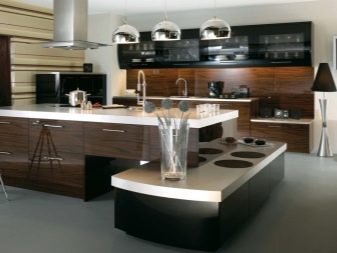
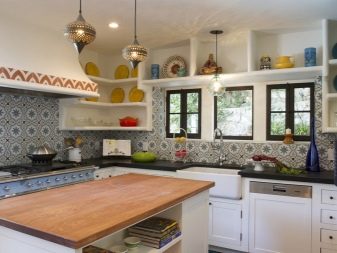
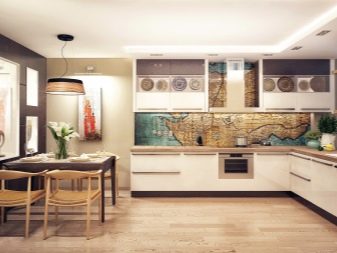
It’s worth thinking about how the countertop will be used. In many cases, housewives are engaged in cutting food directly on it, and so that scratches and other mechanical damage that do not catch the eye should be given preference to a matte plate with a motley color that will hide the defects that have appeared.
Finally, it is important that the chipboard itself be of the highest quality. Pay attention to the detailed characteristics indicating the degree of water resistance and emission class, if there is no such information at all, this is already a hint that the product was made just as.
Among other things, make sure that your copy is new and not damaged during the delivery process.
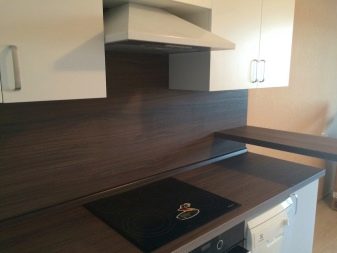
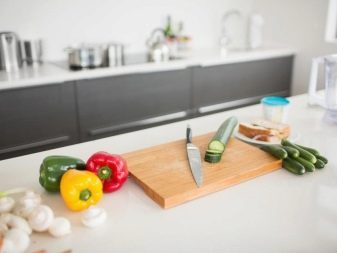
Operation and maintenance
Particleboard is very afraid of water, because it is important to monitor the integrity of the lamination layer, especially in those places where the countertop is adjacent to the sink and hob. If depressurization is detected, it is necessary to repair the panel as soon as possible, using a special sealant.
It is unacceptable to put any hot utensils on the countertop from wood chipboard without using a thermal insulation stand - By this you are very likely to “kill” the panel. Although the chip filler itself is not afraid of high temperature, the latter can melt the plastic protective layer, and it will not only be ugly, but also dangerous due to the risk of moisture penetration. By the way, frozen foods can not be spread on it either - the cold provokes peeling of the plastic.
On plastic countertops, it is not recommended to cut food, otherwise the surface may be damaged.
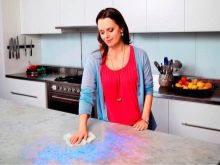
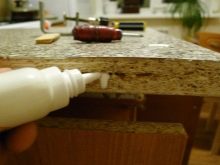
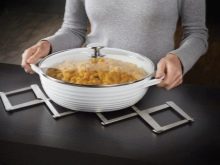
About the tabletops from chipboard for the kitchen, see the next video.